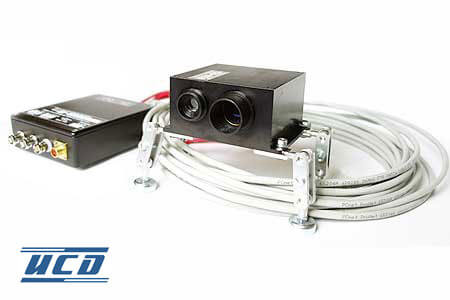
Sensorika-M LLC from Russia is one of the few domestic developers of non-contact track and speed sensors, both optical and laser. Its measuring equipment uses unique technical solutions to significantly improve measuring accuracy.
Systems based on these sensors are highly demanded in the automotive and vehicle testing, logistics, piping, steel-rolling, cable, and other industries. Moreover, domestic developments are much cheaper for the consumers than their foreign counterparts. They at the same time are not inferior to them in specifications, and in some respects even outperform due to the use of not only well-known best practices but also original proprietary solutions.
The optical monoblock, as one of the solutions, is worth detailing. The optical monoblock for the laser sensor, based on the principle of beam splitting by wavefront, provides a stable interference pattern insensitive to temperature changes with zero beam difference, which provides maximum contrast of the strokes in a large range of distances to the object. This does not require any operations to correct the optical unit.
ISD-5
ISD-5 laser system for measuring length and traveled distance is designed for non-contact measurement in the metallurgical, cable, chemical, pulp, paper, textile, and woodworking industries in automated control systems, cutting and accounting, as well as to control the linear speed of vehicles.
laser system for measuring length and traveled distance is designed for non-contact measurement in the metallurgical, cable, chemical, pulp, paper, textile, and woodworking industries in automated control systems, cutting and accounting, as well as to control the linear speed of vehicles.
The laser interference measuring principle is applied, which is based on the technique of speed measurement with a spatial filter. The surface of the measured object is irradiated by two separated and modulated laser beams directed at an angle to each other, which produces an interference pattern (grating) that creates a spatial filter. The reflected signal becomes modulated, and its frequency will depend on the speed of movement of the controlled object. The length is calculated as the integral of speed over time.
PTP Sensorika-M currently manufactures produces two versions of ISD-5 with different working configurations to provide nominal working distances to the object from 20 to 1,300 mm. Upon customer request, custom configurations with different parameters can be also supplied.
ISD-5
- wide range of nominal distances to the surface: from 20 cm to 130 cm and more.
- original monoblock beam divider, which provides stability of the interference pattern and a wide range of acceptable changes in the distance to the object (up to ±25% of the nominal).
- temperature-compensated design providing measurement stability over a wide temperature range without thermal stabilization of the meter. No temperature drift in the meter range +15...+50 °C. Thermal stabilization system (optional) can be used at low temperatures.
- low power consumption (0.5-2 W depending on the used laser) and microcontroller signal processing unit (1 W).
- wide dynamic range of object illumination (from darkness to bright sunlight) and insensitivity to sudden changes in illumination (including fluorescent lighting) and object brightness.
- Small size and weight of the sensor (300-400 g), protection class IP67.
ISD-3
The optical system ISD-3 is designed for high-precision and non-contact measurement of speed and distance travelled by a vehicle relative to the road (in the transport industry) as well as for measuring speed and length of materials moving relative to the sensor in various industries.
The measuring principle is raster spatial filtering of the object image. The serviced object is illuminated by a homogeneous source (bulb or LED), and the periodic structure (raster) is located inside the sensor. This type of ISD becomes a raster spatial filter for the image of the controlled object.
The main distinguishing features of the ISD-3:
- precision measurements: 0.05 - 0.15 %
- wide range of nominal distances to the surface: from 20 cm to 150
- greater luminosity of the optics as no aperture needed. As a consequence, a 10 W halogen bulb and in many cases even 1.2 W IF diode is enough to illuminate the object
- wide dynamic range of object brightness, which can change up to 100,000 times, and sudden brightness changes do not distort measurements
- low sensitivity to optical contamination
- lightweight yet strong and sealed housing, environmental protection class IP67
FIELD OF APPLICATION IF ISD-5/ISD-3
As industrial devices, ISD-5/ISD-3 meet all stringent requirements and standards for electromagnetic compatibility and laser safety. However, analyzing the differences in design features and operating principle, it should be noted that ISD-3 is better fitted for use outdoors and under harsh climatic conditions (wide temperature range, high humidity, dustiness). The optical sensor can measure higher speeds at higher object fluctuations and has very low sensitivity to contamination. ISD-5 laser sensor is more suitable for enclosed spaces, e.g. in the shops of industrial enterprises for cutting and metering systems. Contamination is critical for this device because it greatly distorts the periodic structure at the controlled object. The laser system makes it possible to measure small velocities of controlled objects or small lengths, as well as to make vibration measurements of transverse vibrations with high resolution.
TWO-DIMENSIONAL PERSPECTIVE
Currently, the manufacturer is in the final stage of development of a new high-tech product provisionally called a two-dimensional (two-axis) 2D sensor.
The currently available ISD-5/ISD-3 measure only a straight path in one direction: forward or backward. The new system is designed to measure movements in both directions. For this purpose, the 2D structure is equipped with an additional reversing sensor. The movement direction in the two-dimensional system will be determined autonomously by the optical signal. According to M. I. Makarenko, Director General of PTP Sensorika-M, the main design feature of the novelty is that the measurement system will use the positioning of three sensors, each of which measures in its range and also the vector of speed. Thus, not only the direction of motion and linear velocity will be measured, but also the velocity vector at any point in time. Knowing its value, it is possible to build a movement trajectory of the controlled object relative to the starting point of calculation.
In fact, the 2D system is able to provide the so-called local navigation inside closed rooms and areas without any additional equipment or direction tags. With the dual-axis sensor, the necessary trajectory will be built, due to which any unit of the vehicle will be able to work autonomously as a self-moving robot. Self-propelled carts, cars, forklifts, stackers, and other autonomous robotics will obtain an error-free and interactive map of movements in huge warehouse hubs without the use of satellite navigation.
Local navigation is quite a promising direction for robotic vehicles. Foreign developers are trying to implement such products, but their solutions at this stage remain very expensive. Therefore, the domestic 2-D system has broad prospects for use not only in our country, but also abroad. With the introduction of vector measurement there is no need to use GPS navigation and cluster room orientation. This means that in the near future there will be no need to install expensive floor sensors and reflective equipment inside the huge areas of modern warehouse complexes, as the two-axis system will independently build a movement trajectory relative to the movement surface, relying on the trajectory dynamic measurements of their own sensors.
Local navigation is quite a promising direction for robotic vehicles. Foreign developers are trying to implement such products, but their solutions at this stage remain very expensive. Therefore, the domestic 2-D system has broad prospects for use not only in our country, but also abroad. With the introduction of vector measurement there is no need to use GPS navigation and cluster room orientation. This means that in the near future there will be no need to install expensive floor sensors and reflective equipment inside the huge areas of modern warehouse complexes, as the two-axis system will independently build a movement trajectory relative to the movement surface, relying on the trajectory dynamic measurements of their own sensors.
The design of sensors and their specifications are constantly improving due to the fruitful research work of the company's experts, so we hope that in the near future we will introduce our readers to new advanced and promising developments.