Отчет по результатам измерений длины горячей трубы (около 1200 ºС) лазерным датчиком скорости и длины ИСД-5. Датчик помещён в охлаждаемый водой защитный кожух на расстоянии до 1,5 метра от движущейся горячей трубы.
Объект – труба диаметром 50 мм. На входе приемника измерителя ИСД установлен интерференционный фильтр для подавления теплового излучения трубы.
Область измерения.
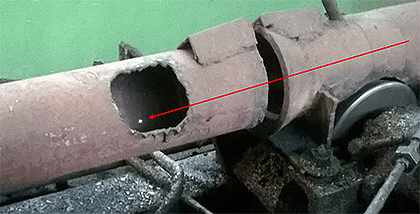
Предыдущее более детально. Видно пятно измерительного лазера (белая точка).
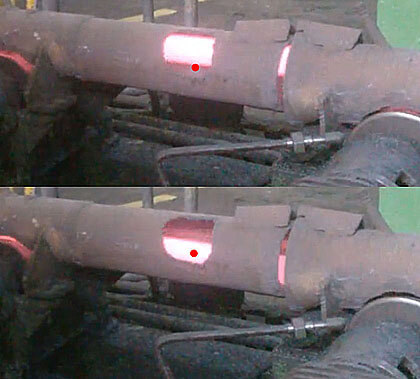
Прохождение трубы. Вверху – начало трубы, виден подскок ее начала на рольганге. Внизу – стационарное положение при движении. Красное пятно – положение лазерного луча.
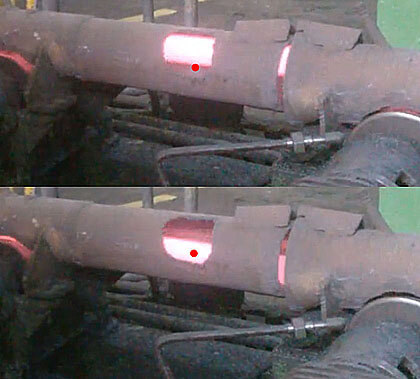
Еще пример, с другого ракурса: Вверху – начальный подскок трубы, она полностью ушла из измерительного пучка.
Это видно на магнитофонных записях сигнала измерителя ниже
Замер длины трубы. Видны два подскока в начале трубы и выброс измеренной скорости в конце трубы (известный эффект, связанный с отклонением отраженного пучка на неровностях конца трубы). Суммарная измеренная длина занижена за счет первых провалов.
Включение медианного фильтра позволяет уничтожить сбои измерений, измеренная длина близка к реальной (с принципиальной неопределенностью, связанной с частотой измерений (см. далее).
Включение усредняющего фильтра на измеренную длину не влияет.
Дальнейшее увеличение медианного фильтра слегка, на 2 мм уменьшает измеренную длину, но зато гарантированно устраняет провалы при подскоках.
Но еще большее значение медианного приводит к существенному уменьшению, здесь – на 20 см. Поэтому оптимальным для данного процесса считаем величину медианного фильтра 10 – 15 (в контроллере по умолчанию установлено 10).
Для справки: спектры сигнала. Типичная форма сигнала для холодного объекта, т.е. тепловое излучение при 1200 ºС не вносит дополнительных шумов
Казалось бы, все хорошо. Но есть принципиальные ограничения измерителя, которые (и пути их преодоления) описаны ниже:
Есть два режима типа объектов
1) Непрерывный – линия экструдера или кабель/металлическая полоса… - и их нужно порезать на мерные куски. При этом датчик работает в стационарном режиме и отсчитывает длину на импульсном выходе с типичным разрешением 1 мм, что позволяет нарезать длины около 1 м с точностью ±1 мм, или 10 м с точностью 3 мм или 100 м с точностью 10 мм ( квадратичная зависимость) – конечная точность определяется уже исполнительным механизмом. Принцип формирования импульсного выхода, практически независимого от частоты измерений, описана в файле «Об измерении длины датчиками скорости.doc».
2) Измерение длины конечных, уже порезанных объектов (выходной контроль). И здесь на первый план выходит параметр длина – скорость движения, поскольку само измерение скорости требует определенного времени, типичное значение – 20 мс (частота измерений 50 Гц). Если объект достаточно длинный и скорости движения низкие – проблем нет. Но ясно, что объект длиной 1 м, движущийся со скоростью 10 м/с измерить с достаточной точностью невозможно, поскольку за время измерения 20 мс он проходит 20 см, а сама неопределенность измерения составляет ±1 измерение в начале и в конце объекта, т.е. ±40 см . Неопределенность связана с тем, что за время измерения объект может появиться в поле зрения датчика к концу этого времени – тогда его сигнала в данном цикле измерения может не хватить, и датчик зафиксирует скорость только в следующем цикле измерения. Тот же эффект будет для определения скорости в конце объекта. Плюс на краях объекта возможны паразитные отражения лазерного пучка на неровностях краев, искажающие измеренную скорость.
Для кардинального решения проблемы точного измерения длины конечного объекта при произвольных длинах/скоростях используются т.н. оптические ворота, т.е. дополнительные датчики, в идеале мгновенно реагирующие на края объекта, расположенные на известном расстоянии, меньшем минимальной ожидаемой длины объекта. При этом датчику скорости нужно измерить только превышение реальной длины объекта расстояния между краевыми датчиками. Подробно это описано далее:
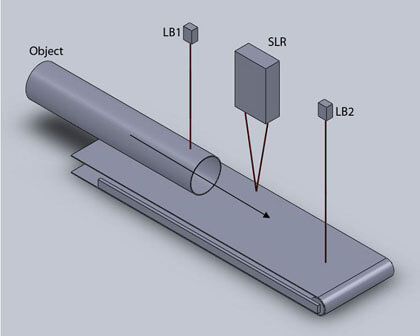
Пояснения
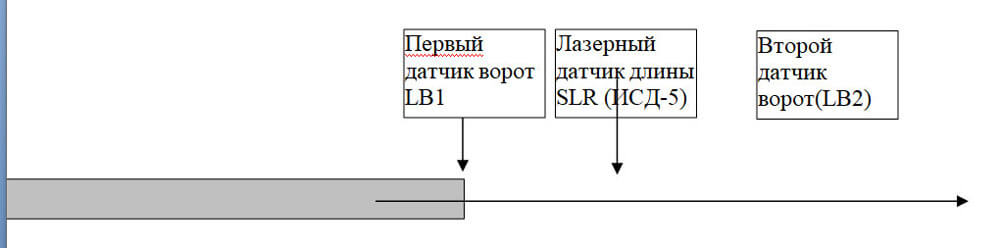
Начало измерения длины: Труба перекрыла первый датчик. Сигнал с него передается на контроллер Сименс с временем реакции порядка 1 мс. Сам датчик ворот также должен иметь быстродействие 1 мс.
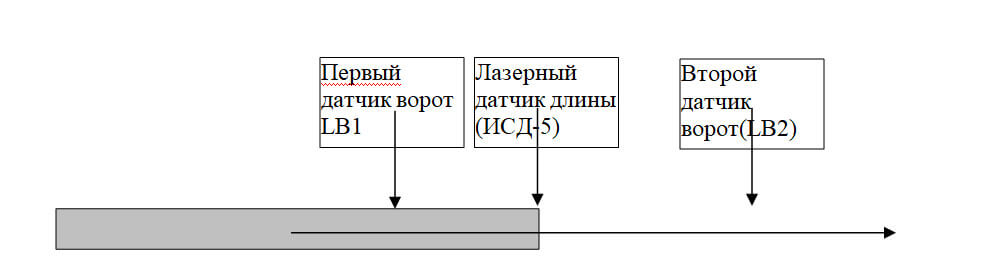
Труба достигла лазерного датчика длины. Он начинает измерять длину и генерирует импульсы с разрешением 1 мм. Но контроллер Сименс пока их не считает.
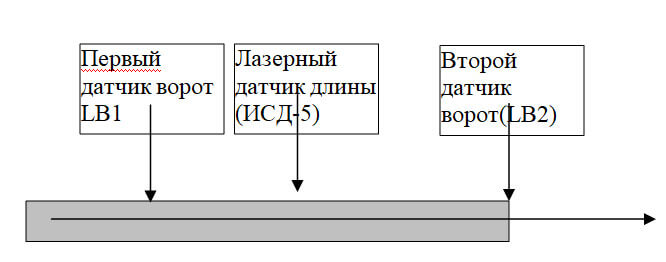
Труба достигла лазерного второго датчика ворот. По этому сигналу Сименс начинает считать импульсы с лазерного датчика.
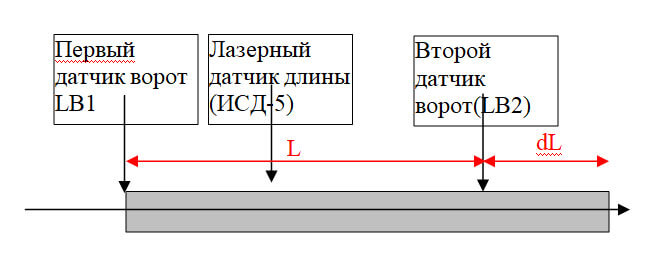
Труба вышла из поля зрения первого датчика ворот. По этому сигналу Сименс прекращает считать импульсы с лазерного датчика.
Расстояние между воротами L известны контроллеру Сименс. К этому расстоянию Сименс добавляет длину dL, которую насчитал по импульсам лазерного датчика. Главное здесь то, что удаляются все краевые эффекты, к моменту, когда сигналы с лазерного датчика считываются контроллером, он уже работает в установившемся режиме и его данные достоверны (и труба к этому времени уже не прыгает). В идеале это позволяет надежно измерять длину с точностью 1 мм (разрешение импульсного выхода лазерного датчика, который можно выставить и 0,1 мм) при любой длине объекта. Реально разрешение уже ограничено точностью измерения расстояния между воротами.
По контролю реальной длины трубы, после ее остывания:
КТР железа считаем 1,2*10-5 / ºС (взято из Инета). При остывании на 1000 ºС получаем относительное уменьшение длины 1,2*10-2, т.е. 1,2%, что при 40 м дает 48 см. Это, конечно, необходимо учитывать при проверке правильности измерения.
Выводы
- Датчик ИСД-5 работоспособен при измерении длины горячей трубы с температурой 1200 ºС
- При необходимой по ТЗ точности измерения (±35 мм на общей длине 40 м, т.е. 0,1%) необходимо использование дополнительных световых ворот. Даже при частоте измерений 75 Гц (разогнал ее до максимума в присланном новом контроллере ИСД-5) неопределенность длины за счет краевых эффектов составляет в худшем случае ±70 мм.
- Подскоки трубы могут представлять проблему даже для световых ворот. Их нужно располагать максимально вертикально (поперечные перемещения трубы меньше подскоков). То же относится и к лазерному датчику. Тем более это актуально при изменении диметра труб. При текущем расположении датчика (см. первое фото) – на минимальном диаметре 30 мм она может оказаться вне поля зрения лазерного датчика (и ворот).
- Крепеж датчика должен быть максимально жестким. Рекомендуется добавить к конструкции термокожуха (там просто стопорные гайки, для видеокамеры этого, может быть, достаточно, но для лазерного датчика нужна большая жесткость и более плавная регулировка, например, упор регулируемой длины (см. первое фото, зеленая стрелка).
Отчет подготовил:
Растопов Станислав Федорович,
к. ф.-м. н., тех. спец. ООО «Сенсорика-М»